Wind turbines have a “big” problem. As in, they’re really big: bigger than you might think. One of the latest turbine designs sports a swept area of about 10 American football fields.1 This is generally desirable, especially for offshore turbines. But as you can probably imagine, this makes producing, transporting, and installing these things a colossal undertaking. And as turbine manufacturers have competed against each other, the push to maximize size has ended up undermining quality.
This has led to defects and mechanical failures. Just look at the recent news around one of the world’s largest wind turbine companies, Siemens Gamesa. And when machines stand taller than world wonders, you don’t want them — or hope in renewables — to come crashing down. All is not lost, though. There’s some exciting progress being made to address those downsides, like 3D printing, new automation technologies, and some other really cool stuff.
So, how can we fix wind turbines’ current conundrum?
If you follow clean energy news, you’re probably familiar with the trouble that’s recently plagued Siemens Gamesa, one of the world’s most prominent turbine manufacturers. The company has been on the receiving end of intense financial blowback this year, starting all the way back in January. That month, its parent company, Siemens Energy, was sweating under the spotlight after needing to make hefty cuts to this year’s profit outlook. Siemens’ loss of 472 million euros (or $512 million) accounted for the cost of addressing faulty components it discovered across multiple turbine models — both onshore and offshore.2 These issues include wrinkles on the blades and particles in the turbine bearings, and Siemens estimates that they affect 15% to 30% of its latest 4.X and 5.X turbine platforms.3
Then, in June, things took a turn for the worse when Siemens had to toss out its 2023 profit outlook completely. The company not only announced that the defective parts could require over 1 billion euros to fix, but also acknowledged that correcting the flaws would take years.4
Notably, the day after Siemens delivered the bad news, shares in the European manufacturers Vestas and Nordex took a dive as well.4 It goes to show that Siemens isn’t the only major turbine manufacturer in jeopardy — it just happens to be the one catching the most publicity right now.
This situation got me curious. What aspects of turbine design and manufacturing can we improve? There’s some really cool solutions hitting the market, like SkyBAAM, which is using additive manufacturing to make wind turbines onsite. There’s another company going the route of multi-rotor wind turbines, which means going smaller, not bigger. But before we get into those, we really need to break down why these changes need to happen.
In the past few years, the entire wind industry has been facing structural problems…literally. From supply chain obstacles to defects that escape detection on the factory floor, wind tech has been under increasing scrutiny as it’s buckled under the pressure to expand. These issues have been evident across the United States and Europe, and haven’t spared any of the Western world’s key manufacturers, including Vestas, General Electric (GE), and Siemens.5
And stocks in wind manufacturers haven’t been the only thing falling, because a concerning number of turbines have been abandoning their posts. In September 2021, a 784-foot-tall tower (~239 meters) manufactured by Nordex fell over in Germany just a few hours before it was supposed to be inaugurated.67 In June 2022, a GE turbine less than a year old collapsed in Oklahoma. A few days later, another turbine of the same model toppled over in Colorado.5
What the heck is going on? The problem is that the direct causes for the failures aren’t published, so it’s hard to pinpoint the exact causes. However, the consensus among many industry experts is clear: The core issue stems from the rush to enlarge turbines further and further for the lowest cost possible, which has been exacerbated by the increasing urgency to transition to clean energy. This ultimately took precedence over the need to maintain the technology’s reliability. As a result, despite the fact that the whole point has been to increase turbine height, it’s been a race to the bottom, not the top.5
As GE CEO Larry Culp said last October, “It takes time to stabilize production and quality on these new products. Rapid innovation strains manufacturing and the broader supply chain.”8
Manufacturers’ misaligned priorities aren’t all to blame. A number of other factors have contributed to these incidents. According to reporting published by Bloomberg last April, manufacturer profits haven’t kept up with mounting demand. The article cites “high raw material and logistics costs, changes in key clean-power subsidies, [and] years of pressure on turbine prices.”9 And demand is only going to continue to accelerate. Just within the U.S., the need for turbine components is expected to multiply five times over throughout the upcoming decade, according to a Department of Energy estimate.10
On top of all this, there’s unique circumstances that make producing wind turbines difficult, well, by design. I previously touched upon why bigger is better in the world of wind in my video on towers that float on the ocean’s surface, so if you’re interested in more of the engineering specifics, be sure to give that a watch. For now, it’s important to keep in mind that though it might seem impractical, the math and physics of developing giant turbines does amount to more energy generation on a mind-boggling scale. Like, powering an entire home with a single rotor rotation levels of production.11 However, this massive yield comes with double-edged blades.
That’s because if you think about it, wind turbines exist in a realm of their own. There’s simply no other existing parts that fit this scale of machinery. This means that each model’s components are effectively bespoke, especially as towers grow. You can’t use the same parts between larger and larger turbines because the load is different. It would be like trying to swap an airplane propeller for a pinwheel.
And of course, the considerable amount of organization and resources required to construct and deploy highrise-height devices is another huge hurdle, to say the least. For example, carrying wind turbines safely to their destinations can actually take a whole year of planning.12 As Mark Johnson, director of the DOE’s Advanced Manufacturing Office says:
“We’re really going big. We’re trying to make very large structures. We’re limited by the size at which you can get these parts down a roadway. People see this number every day: 14 feet, 6 inches. That’s the height of a bridge. You can’t make a part bigger than that.”13
These burdensome logistics are especially relevant in the case of offshore wind, as I covered in my previous video. Floating turbines cost twice as much to establish, considering their needs: delicate engineering to keep them aloft, vast networks of submarine cables to deliver electricity, and the incredibly expensive jackup rigs used to install and maintain them.14
So, what’s on the horizon to solve these dilemmas…beyond more rows of wind turbines? Let’s start by going over the big-picture solutions. Manufacturers have already recognized the obvious need to shift focus away from speedy expansion and instead advance their tech’s reliability. Back in January, Vestas CEO Henrik Andersen argued that turbines don’t need to be any bigger and that ramping up production is the name of the game.5
And in Siemens Gamesa’s case, CEO Jochen Eickholt has noted that going forward, the company will be fostering “stability and profitability before growth.”3 The company also said in mid-September that it’ll now be turning its attention to cleaning up the mess on its hands and slowing down sales:
“Our absolute priority is to revise the affected systems in existing customer projects,” a Siemens Energy Group spokesman said. “That’s our focus.”3 5
Another significant path to improved industrialization is automation. The Department of Energy actually just announced the release of nearly $30 million in grants to promote the development of advanced manufacturing procedures, including automation and the additive manufacturing of turbine components.10 Of the 13 initiatives the DOE invested in, 6 concentrate on 3D printing parts, blades or otherwise.15
One of these projects is headed by the California-based startup Orbital Composites. It’s working to simplify offshore wind construction by taking advantage of a new form of 3D printing developed specifically for infrastructure called SkyBAAM, or Sky Big Area Additive Manufacturing. Patented by Oak Ridge National Laboratory (ORNL) in Tennessee, SkyBAAM is essentially a crane robot that uses a system of cables to deposit concrete directly onsite.1516
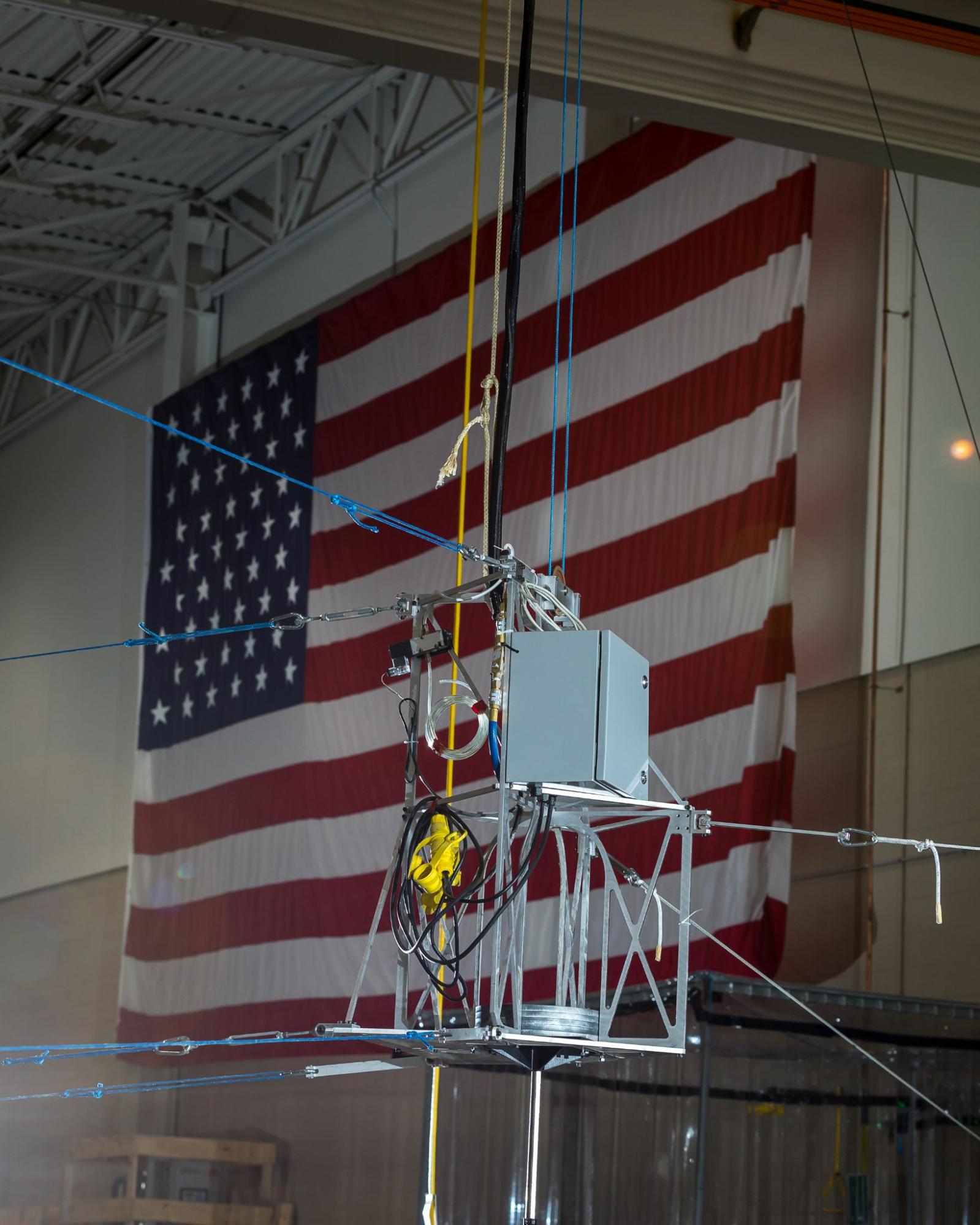
SkyBAAM
This accomplishes several things at once. First off, SkyBAAM’s setup is a lot smaller than the platforms that are typically used for construction. Its convenient size therefore translates into less money and effort spent on getting it from point A to point B. The system also requires less onsite prep, and can be adapted to uneven ground. The way it looks and works is kind of cool. It’s not dissimilar to the skycams that you see in sports stadiums. Anchors and guide wires located around the work area to stabilize and control the print heat in the middle. ORNL estimated in a 2019 report on the SkyBAAM prototype that a, “future full-scale system would be able to print objects with a major dimension of 100 feet or larger.”16 According to the DOE, the robot “can print components 10 times larger than other additive manufacturing machines” at a rate that is anywhere from 500 to 1,000 times faster. Overall, 3D printing the mold reduces manufacturing time by up to 35%.13
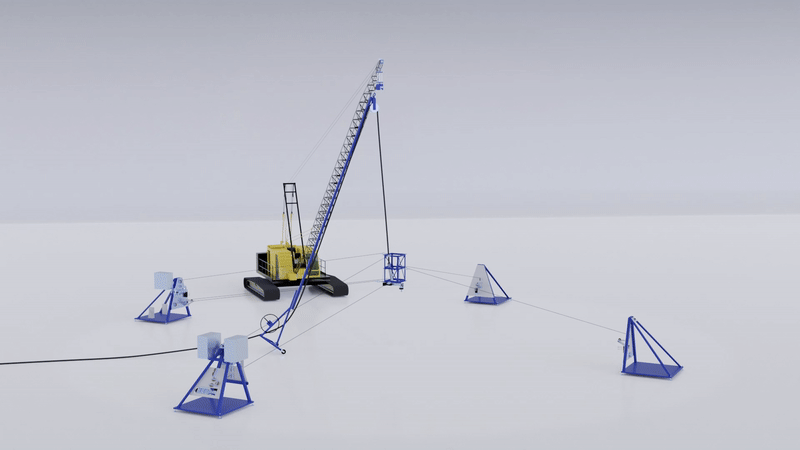
SkyBAAM
The initial SkyBAAM prototype was completed in 2018, and ORNL began using it in projects in 2020.17 Now, Orbital Composites is working to combine SkyBAAM with “ultra-high-performance concrete and carbon fiber reinforced polymer” to do more with less. The goal is to cut costs and the amount of supplies used while also strengthening structural performance.15
Why all the fuss about carbon fiber? 3D printing carbon fiber isn’t exactly new, but at this scale … it is. According to research conducted by Sandia National Laboratories in the U.S., blades made with the stuff are about 25% lighter than those constructed with fiberglass. This means that blades can be built in longer lengths. If you’ve learned anything from my videos on turbines recently, you know why this is advantageous: broadly speaking, larger turbines equate to larger amounts of energy captured. Plus, carbon fiber is also more resistant to fatigue, which extends blades’ lifetimes.18
As for how Orbital is using carbon fiber to cut costs, here’s how the company explains it on its website:
“Our continuous carbon fiber reinforcement capabilities are designed to enable you to apply carbon fiber exactly where you want it. By reinforcing only where necessary, you can create lightweight, strong thermoplastic parts at a significantly reduced price compared to current carbon fiber manufacturing technologies.”19
Basically, 3D printing enables cheaper construction through its precision: by only extruding the material you need, nothing is wasted. The company anticipates that this will come out to a cost reduction of 25% — not including the additional 10% to 25% that’s saved by avoiding the rigamarole of maneuvering completed blades during transit. Another future benefit is the ability to use recyclable material to 3D print blades. This is a big deal, because the majority of wind turbines can’t be recycled, and that’s a quickly intensifying problem as decommissioned blades pile up.1220
Orbital also will be putting its own fleet of printing robots to the test, which are containerized so that they can be easily carried via shipping containers and dropped off onsite. They’re like mini-factories on wheels. This has important potential implications for offshore wind specifically, which is heavily reliant on cranes.21 As co-founder and CEO of Orbital Amolak Badesha says:
The sheer scale of off-shore deployment vessels is an impressive feat, one unmatched by terrestrial cranes. Cranes big enough for land-based, 100-meter-long blades do not exist,” Amolak says. “If the shipping containerized factory can be placed directly beneath the tower, then blade hoist and repair systems may be incorporated into the shipping container superstructure.”21
Keystone Tower Systems, a Colorado company founded by Massachusetts Institute of Technology researchers, is also making noteworthy strides in automation. The company invented a new patented form of turbine tower that’s assembled using spiral welding. What makes it so special? Well, you only need one machine to complete several stages of the manufacturing process in one smooth operation. The equipment rolls sheets of steel like Pirouline wafer cookies into towers that are lighter and cheaper, but just as capable.2223 Not too tasty, though.
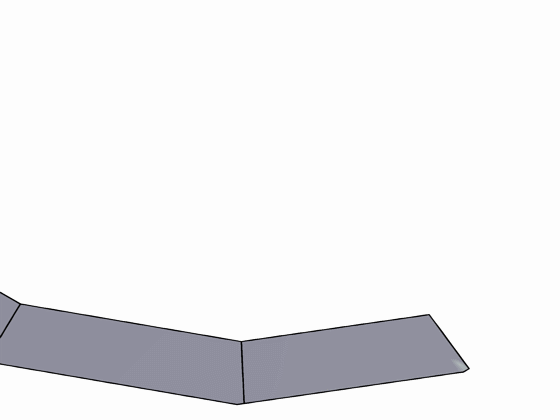
Keystone Tower Systems manufacturing method
The company also claims that their manufacturing method is 10 times faster. Even better, the machine can be set up to produce the towers onsite in less than a month, skipping the headache of moving towers on the road.2223 Keystone rolled out its first towers in 2022, and its next move is to install the largest tower in the States in partnership with the DOE.24
But just like any strategy, automation isn’t an all-encompassing quick fix. As cool as it would be to spit out turbine pieces with the push of a button…it’s more complex than that. And you can’t automate everything. Take it from John Korsgaar, Senior Director of Engineering Excellence at Danish company LM Wind Power. During a 2021 presentation on blade manufacturing, he explained that the specialization of factory machines limits their value. He points out that automated equipment is often really pricey, requiring it to be running constantly in order for companies to see returns on their investment. In contrast, we humans naturally have the flexibility to learn how to complete multiple kinds of tasks. It’s simply more cost-effective, Korsgaar argues, to keep your workers of the flesh variety.25
Now for the really fun stuff: new variations of towers in unconventional shapes and sizes. I’ve talked about a lot of fascinating companies putting their own spin on turbines, from rooftop-optimized devices like the “motionless” model created by the U.S.-based company Aeromine to the Electrostatic Wind Energy Convertor developed at the Delft University of Technology in the Netherlands. Needless to say, we’ve got plenty of designs out there breaking the mold. But have you ever seen turbines inside of turbines?
Yep, you heard me right. Myriad, a startup formed by three Scottish researchers from Universities of Strathclyde and Edinburgh, is currently developing a multi-rotor wind turbine, or MRWT. It’s made with a cluster of smaller rotors rather than a singular large one, which are housed by a modular frame. It kinda looks like a flyswatter.26

Myriad MWRT
Like the other emerging technologies we’ve gone over so far, the MRWT is assembled onsite. The much more compact blades also neatly fit inside standard shipping crates, making transportation…a breeze.27
Besides the easier installation, why incorporate more rotors into one turbine? According to the team, “there’s an economic and technical limit” to the size of blades and towers, “and we’re beginning to reach it.” By greatly reducing the volume of the blades, according to the researchers, you minimize costs. You also boost performance by arranging the rotors into an array because of the square-cube law. Wind turbines can suffer from something called the blockage effect, which is when one turbine reduces and alters the wind speed and direction that hits another turbine further downwind. That ultimately decreases the amount of energy captured. It’s kind of like sharing a milkshake with your significant other and they’re sucking up way more of the milkshake than you are — leaving you with bits of the leftover dregs and an empty stomach. The MRWT design helps to alleviate some of that and capture more energy than a conventional turbine.26
So, even though wind energy is struggling to regain its footing at the moment, there’s still a lot to look forward to. The challenges we’re facing are indicative of a need to change gears, but you could say the industry-wide stoplight is yellow, not red. It’ll be interesting to see what innovations arrive on the winds of change.
- CSSC Haizhuang H260-18MW offshore wind turbine giant emerges ↩︎
- Siemens Energy cuts profit outlook on wind turbine woes ↩︎
- What’s the problem with Siemens Gamesa’s onshore wind turbines? ↩︎
- Siemens Energy’s shares tumble as wind turbine troubles deepen ↩︎
- Wind Turbines Taller Than the Statue of Liberty Are Falling Over ↩︎
- Germany: Wind turbine collapses hours before official launch ↩︎
- Tower ‘weak points’ to blame for German wind turbine collapse: Nordex probe ↩︎
- Giant Wind Turbines Keep Mysteriously Falling Over. This Shouldn’t Be Happening. ↩︎
- Wind power’s ‘colossal market failure’ threatens climate fight ↩︎
- DOE Announces $45 Million To Innovate Manufacturing For Wind And Water Energy Technologies ↩︎
- Haliade-X offshore wind turbine ↩︎
- This startup is using robots to 3D print giant wind turbine blades ↩︎
- Transforming Wind Turbine Blade Mold Manufacturing with 3D Printing ↩︎
- Annual Technology Baseline: Offshore Wind ↩︎
- Funding Selections: AMMTO Large Wind Turbine Materials and Manufacturing Funding Opportunity Announcement ↩︎
- SkyBAAM Large-Scale Fieldable Deposition Platform System Architecture ↩︎
- SkyBAAM – an innovative process of 3D printing from concrete ↩︎
- Carbon fiber for wind turbine blades could bring cost, performance benefits ↩︎
- Epic End-Effectors ↩︎
- Wind Turbine Blades Can’t Be Recycled, So They’re Piling Up in Landfills ↩︎
- Orbital Composites to demonstrate containerized 3D printing robots for AM wind blade manufacture ↩︎
- Spiral Welding ↩︎
- Onshore Towers ↩︎
- Keystone Tower Systems: About Us ↩︎
- Industry perspective on manufacturing of future large wind turbine blades ↩︎
- The future of wind energy is modular ↩︎
- Myriad Wind Energy Systems ↩︎
Comments